

Karen Willcox: The community has high-fidelity computational models that aid in making these predictions, but those models are so complicated that they take a very long time to simulate. Tech Briefs: What models are currently available? What are the drawbacks of traditional rocket design/simulation methods?
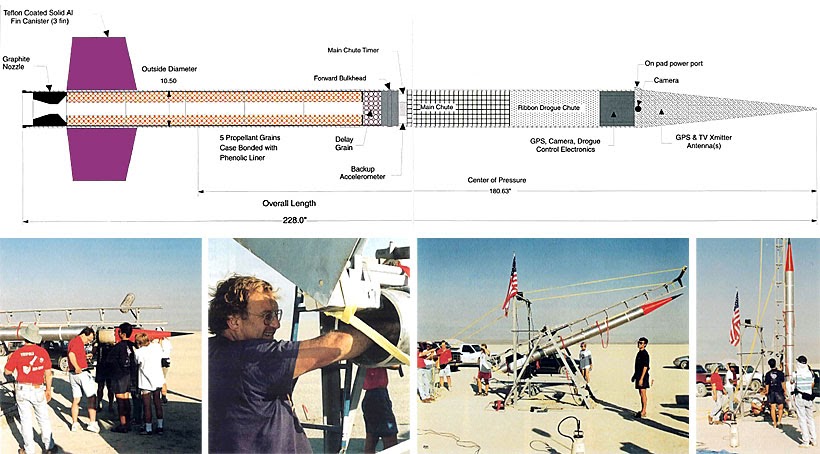
For example, we need to be able to understand how a change in injector geometry will alter the complex flowfield inside the injector. To make good design decisions, engineers need good predictions of how the engine will respond.

Karen Willcox: We are addressing computational cost. Tech Briefs: What is your simulation method doing better than alternative rocket design software? In an edited interview via email below, Director Willcox tells Tech Briefs about her team's efforts to quantify uncertainty for a system as complex as a rocket engine. “They provide answers good enough to guide engineers’ design decisions, but in a fraction of the time.” “These reduced-order models are surrogates of the expensive high-fidelity model we rely upon now,” Willcox said. Karen WillcoxĪlthough not perfect, says Willcox, the models do an excellent job of predicting overall dynamics, and are particularly effective at capturing the phase and amplitude of the pressure signals - key elements for making accurate engine stability predictions. Big decisions need more than just big data, they need big models too. While the GEMS "training" takes about 200 hours of computer processing time, the reduced-order models can run the same simulation now in seconds, and can be run in place of GEMS to issue rapid predictions.īeyond repeating the training simulation, the models also can predict how the combustor will respond to operating conditions that were not part of the data set. Each picture represents a variety of launch parameters, including pressure, velocity, temperature, and chemical content.
High power rocket simulation code#
The snapshots, generated by an Air Force combustion simulation code known as General Equation and Mesh Solver (GEMS), serve as the training data for the system and the reduced-order models it produces. The "scientific machine learning" approach, led by Oden Insitute director Karen Willcox, provides makers of rockets with a fast way to assess engine performance in a variety of operating conditions.

"This is highly desirable in today’s environment where designers are heavily constrained by cost and schedule.” “In some important cases, these reduced-order models are the only means by which one can simulate a large propulsion system," said Ramakanth Munipalli, senior aerospace research engineer in the Combustion Devices Branch at Air Force Rocket Research Lab. The system, developed at the Oden Institute for Computational Engineering and Sciences and and the Massachusetts Institute of Technology, uses "snapshots" of physics data to create reduced-order models - simulations that run very quickly and are therefore valuable for rocket builders looking to try out a variety of designs. To speed up the design process, researchers from the University of Texas are finding more efficient ways to predict, or "learn," a rocket's behavior. When you're testing the stability of a rocket, you can't just fire up a design.įactors like temperature, pressure, and velocity impact a rocket's journey, and the parameters must be examined and modeled.Įven computational simulations are done for weeks or months with a supercomputer, given the stakes of such a complex and explosive application.
